The speed controller measures out current and battery voltage to the electric vehicles’ motor to raise and lower speed on the golf cart. It monitors the state of the motor and generates signals to match the alternating currents.
With the newer AC motor or Brushless DC motor technologies, the electric golf cart motor will not operate at all without a speed controller. These motors now require reversals in current that are accurately timed with the motor’s rotation. The purpose of the controller is to generate the exactly timed signals the motor requires to function.
Speed Controllers Are Important
Without the ability to measure out varying amounts of voltage, the motor would be either on or off, with nothing in-between. If you pressed the pedal, the golf cart would jackrabbit jump to full throttle.
Control of the old-style DC motor was accomplished by resistance, usually stepping through three to five different speeds. This was controlled by solenoids redirecting the voltage through different resistance tap points.
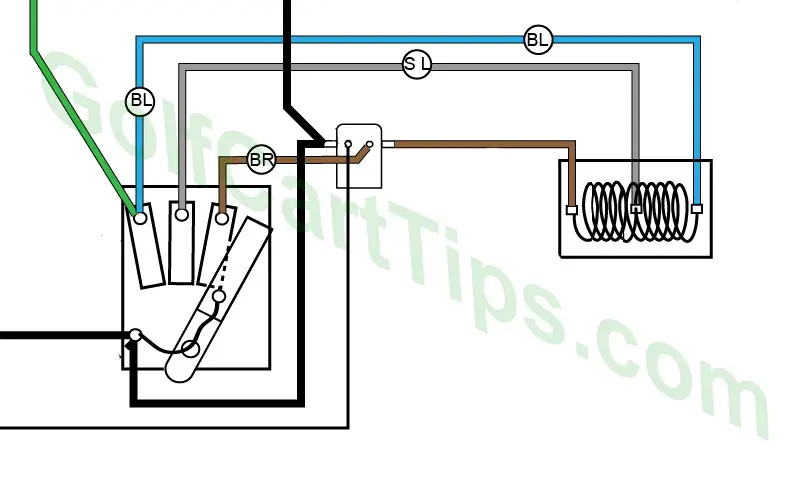
Other methods of controlling the motor were to change battery voltage by re-routing different groups of the six batteries with solenoids. Three of the 6-volt batteries would be 18-volts, or in the case of 36-volts, half power. Low Speed would be 18-volts through a resistor. 2nd speed would be 18-volts without the resistor. 3rd speed would be 36-volts through a resistor, etc.
The speed controller today is itself controlled by the cart operator employing a varying amount of electrical signal. This signal is sent by a pedal-driven resistor or throttle inductance coil.
Speed Controller Functions
As the name implies, the speed controller will change the golf cart speed to the golf cart driver’s preference, but because of advances in technology, it does much more.
The speed controller can offer the following functions:
- A controlled ramp up to speed if the full throttle is applied suddenly. From a standing start, AKA locked armature, a motor can initially take up to 20 times its normal operating current. This must not last more than a second or two to avoid damage to the system.
- Protection from ground faults caused by accidental shorts.
- Safely reversing the motor by taking the motor to a stop, then reversing polarity.
- An overheating protection thermal shutoff to protect the controller from damage.
- Battery voltage monitoring to prevent the complete drain of the charge.
- Overcurrent limiting to protect the motor and electrical components from damage.
Some speed controllers even allow independent programming to change the basic functions, especially top speed. Just how customizable your controller is will be dependent on whether your electric vehicle is a Series system or a Shunt system.
How A Speed Controller Works On An Electric Golf Cart Motor
On a golf cart, pressing the accelerator pedal down does two things…first, a microswitch energizes the system by activating a powered solenoid. Second, the linkage either operates a potentiometer or a plunger that passes through a Throttle Position Sensor. This sends a variable electrical signal to the controller. This signal, based on the strength it sends, tells the speed controller what level current to send to the motor.
The Difference Between A Series And A Shunt system.
Club Car’s Power Drive is a Series Motor System, on the market from 1990 and up. On the golf carts built in the years 1990 – 1994, the controller used a 0 to 5K potentiometer (36 Volt). In the years 1995 and up, they used 5K to 0 potentiometers (48 Volt).
A shunt motor system is also known as a Regen and referred to as a Sepex (Separately Excited). DCS (Drive Controller System) was in use 1995-1999 and was the first shunt-wound motor system. It was controlled by a DCS Controller. This motor did not have a sensor and the controller did not count RPM’s. In 2000 the PDS (Precision Drive System) controller was introduced along with the Regenerative braking, and the motor has a speed sensor and cable to interact with the speed controller.
A Series motor has no speed sensor. It is a completely different circuitry from the shunt system, even with the older shunt-wound models’ lack of a speed sensor.
E Z Go offered a Series System and controller from 1988 to 1994.5 and a Non-DCS Series Motor System from 1994.5 and up.
Yamaha G8 (1990) to the G16 (1996) is a Series Wound Motor System, with the Shunt Wound Motor Systems being introduced with the G19 (1996) to the G29 (2007).
Note: AC Motors
There are also AC Motor (Alternating Current) systems available on the E-Z-Go RXV and late model Yamaha golf carts. AC motors and their operations are yet another completely different set of speed control components.
You can convert a stock DC motor over to an AC and gain the following control over the motor:
- Acceleration control
- Maximum speed control
- On-the-Fly programming
- Speed limiting
- Motor/controller thermal protection
- Regen control for forward and reverse – useful when driving or backing on inclines
- Rollback protection
- Some models even offer Bluetooth programming
With Bluetooth, your smartphone will act as the vehicle instrument panel. The app allows Remote locking of the vehicle and recording of diagnostic data for troubleshooting help and maintenance.
Using A Speed Controller In A Custom Build Golf Cart
A stock two-passenger electric vehicle will have a standard 200-300 amp controller coupled with a 2-5 horsepower motor. This is adequate for most flat ground light hauling. Much higher-powered controllers, such as the Alltrax or Curtis brand, can be paired with larger horsepower motors for speed and performance on hilly terrain.
Deciding What Power Rating Your Speed Controller Should Be
When customizing a golf cart for better performance and higher speed, you need to make sure of what system you are working with and what you want to do with the modified electric vehicle. All components need to support each other and the system is only as strong as the weakest link.
Motor type variations will be permanent magnet type, shunt-wound, series-wound, brushed and brushless DC, induction AC, and permanent magnet AC. Battery voltage will range from 24 volts to 96 volts, flooded acid, or lithium-ion.
Tire size will factor into the torque required for your purposes, and increasing the horsepower can mean you need to get a higher amperage controller, solenoids, switches, and cables.
Non-stock speed controllers such as the Altrax and Curtis brand come in different amp ratings, such as 200, 300, 400, and 500 amps. Of course, the larger the amp rating, the more costly the unit.
These speed controllers are custom configurable either with an optional hand-held diagnostic/programmer, or a USB cable and Windows software. RPM and current settings can be customized for your control system.
How Do You Troubleshoot A Golf Cart Controller?
Since the controller is the heart of your present-day electric golf cart, not to mention expensive, you want to make sure that the problems are not something else entirely. Here is a list of items to check before you search for the speed controller diagnostics.
- Check the golf cart battery pack…If it isn’t delivering a full current to the speed controller, then it will not function. Top off the water in all batteries and measure the voltage at the battery posts.
- After checking the power source, check the solenoid. When the pedal is depressed, you should hear a solenoid click. THIS IS NOT a function of the speed controller. It is a separate component that turns the speed controller on. If there is no click, this check should include the microswitch at the pedal as well as the connections going to the solenoid. If you need to do in-depth testing of the solenoid, refer to the article “Bad Solenoid In Your Golf Cart? Here’s How To Test And Fix It”.
- Test the potentiometer if your golf cart uses one. Most golf cart potentiometers are 5K – 0 ohms, and you can get a multimeter to help test its output. 5,000 ohms would be the reading when you floor the accelerator. If your golf cart is an EZ-Go with an ITS (Inductive Throttle Sensor) check the voltage reading with a multimeter. On a DCS – After the solenoid engages, the reading should be .04-.06 through 1.5-1.7 volts at full pedal. On a PDS – After the solenoid engages, the reading should be 1.0 volts plus or minus .03 volts and 2.7V plus or minus 0.5 volts at full pedal.
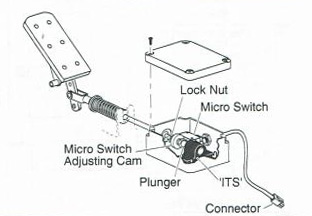
- Any failure in these readings requires a replacement of the unit
Next Steps
If you reach this point and the other components check out properly, the next step is to inspect the speed controller itself. Ensure all cabling and connections are tight and secure with no corrosion or arc burns on the connectors.
Most controllers will have a small light that will begin to flash a code sequence that can be compared to the golf cart manual. If the code indicates the source voltage is incorrect, then you will need to go back over the previous steps. If the code indicates a controller fault, then the controller will need a reset, repair, or a replacement order.
Golf Cart Speed Controller Replacement
If you have determined that the speed controller is at fault, you may have to get a replacement. Make sure you get one of the same or compatible controllers for your make and model electric golf cart.
Before beginning to remove and reinstall the new controller, be sure to disconnect all power from the batteries. Next, make a note of which wire goes where and most importantly, don’t allow one of them to touch and short out. Even if the power is disconnected (or you think it is) it is too expensive of a mistake to accidentally burn the new unit out.
Hand tighten all connections and terminals and do not over-tighten because stripped out screws are no fun. After you are certain all connections a correct and secure, reconnect the power and road test your golf cart.
Conclusion
What does a golf cart controller do? As you can tell by this article, plenty! From being able to modify your golf cart speed, to managing all of the electrical components in perfect harmony, the controller really is the “heart” of your golf cart.